Jamdani: its heritage and recognition in the world map
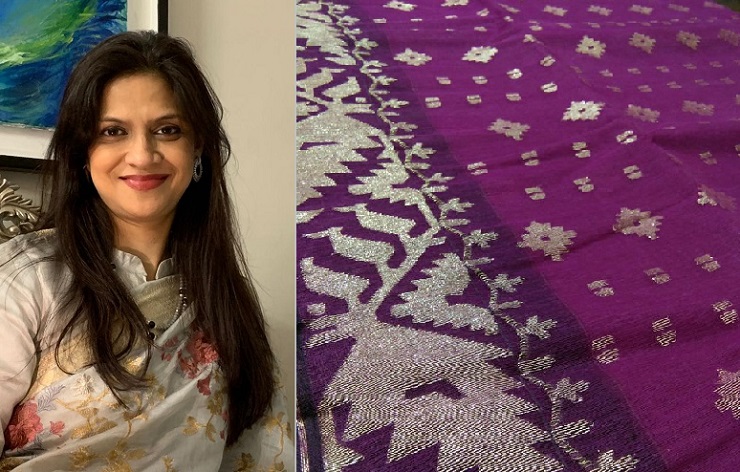
Jamdani is a fine muslin fabric origanted in Bangladesh, not very new in the global map. The opulenceofjamdanidesign not only makes it’s a technical marvel but also guarantees its omnipotence in the handloom industry, no machine could ever surpass its richness.The much appreciated and cherished art of Jamdani weaving of Bangladesh has been duly recognized by UNESCO as the intangible cultural heritage in 2013. It is at the same time a recognition for weavers.
Genesis of it can be traced back to the Mughal era, but it’s place of origin was Sonargaon, Dhaka, Bangladesh. Sonargoan, Bangladesh still continues to be the hub of jamdani or as the local call it jamdanipalli. The word Jamdani has been derived from Persian word ‘Jam’ meaning flower and ‘Dani’ meaning vase. As the name suggests jamdani traditionally had flower motif vividly woven on a loom into the finer fabric by expert craftsmanship.
During the Mughal era, the jamdani and muslin production was at its zenith as it was patronized by the Mughals. The region around Dhaka was naturally blessed with the type of cotton called ‘Kapas’, which could produce fine, long and soft cotton fibres. The Julahas or weaver would then turn this fabric into unparalleled jamdani sarees. The region around Dhaka, between the Old Brahmaputra, Meghna and Shitalakhya rivers was very fertile and suitable for growing this cotton. The water in these rivers were rich in minerals and the soil in the river banks contained sufficient moisture and heat, all of which aided the cultivation. The river water was used to dye and clean the cotton, and its mineral content gave a glaze to the cotton fabric. The network of rivers not only aided in giving the julahas the finest fabric but also in transportation and providing the local and overseas market.
Jamdani is known, not only for the finesse or intricate fabric but also for being overtly priced. The hard work and toil of the weavers are not known by many. The cotton threads are dyed and is strengthened and softened by soaking overnight in a solution of rice water starch, allowing the women to wind it more easily onto bobbins. It is tedious work done early in the morning, usually between 4 and 9, before the increasing heat dries the thread, making it more difficult to handle. The wound bobbins are sent to another worker who prepares the warp on a beam. Afterwards, the warp is sent to the weaver’s house where it is set up on a loom. Interestingly the designs are woven directly into the fabric by a weft technique. Usually two men work at one time on a loom.
During the British colonialism the Bengal jamdani and muslin industries rapidly declined due to colonial import and rise in industrial manufactured products. It was difficult to compete with cheaper industrial product. The weavers toiled harder and suffered greatly as they were unable to match the cost and swift production of machines.Jamdani is labour intensive form of weaving, a final product may take five months or more. The final productof handloom jamadaniwas a product of unparalled technical marvel and finer creativity of the artisan. In their endeavor to keep up the tradition of jamdani, the artisanshave through ages hold on to their exquisite splendor of creativity and passed on to their posterity.
It is craft process that was at verge of extinction, but with the unfaltering efforts of the finer weaver, the fine artistry of jamdani has not died out. The Jamdani Industrial Estate and Research Centre was established by Bangladeshi government as an initiative to improve the jamdani industry. Bangladesh smalland Cottage Industries Corporaration (BSCIC) was set up in 1982, to boost up the jamdani industry.National Crafts Council of Bangladesh (NCCB) since its inception in 1985is engaged in the field of craft research and development. It not only promotes the craft sector but work towards maintaining the originality of craft traditions, benefits the poor weavers in ensuring their livelihood. They have collaborated with the biggest handloom/craft fashion houses of Bangladesh- Aarong, Aranya, Tangail Saree Kutir and Kumudini They organizeJamdani festivals and brings forward different aspect of the jamdani to the people. They tried to recreate the famous “the loom figured Muslin” and the antique designs of Jamdani.
The Craft organizations are also organizing event on their own in promoting Jamdani. The Different Embassies of Bangladesh are also contributing in their own ways to promotingJamdani, the pride of Bangladesh. The Jamdani diplomacy of presenting high officials of different countries is a way to enhance the recognition and appreciation of jamdani in foreign soil. Our growing Bangladeshi diaspora and growing economy has open up the horizon for jamdaniand its popularity, which was otherwise restricted to West Bengal, Tripura and Assam. To make it available to a wider group jamdani is now being made in kurtas, shalwarkameez, Panjabi for menand scarves etc.
Today the Bangladeshi women takes pride in wearingJamdani in national events. Jamdani saree has become a symbol of identity, dignity and self-recognition for Bangladeshis. Others who join the fold of Jamdanifeel it is one the most expensive and delicate fabrics and at the time a symbol of aristocracy.Jamdani makes us feel so Regal.My heartfelt appreciation for all fine artisans who has had hold on to the tradition of Jamdani weaving.
Aouthor: Teacher, Sunnydale Scool, Dhaka.
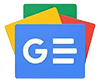
মন্তব্য করুন